图7 A-A方向料头流速分布和变形图(向左边弯曲,且幅度较大)
图8 从A-A视图方向看过去的料头(向左边弯曲,且幅度较大)
(5)型材流速和实际变形分析对照:
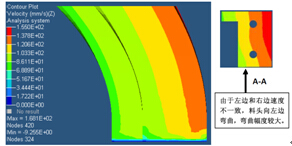
图9 B-B 料头流速分布和变形图 (向左边稍微弯曲)
图10试模结果,C-C视图显示,从C-C方向看过去,型材向右边弯曲;
(1)型材速度和变形模拟分析:整体流速不平衡,相差较大,图3显示, 型材左侧的流速慢,右侧流速较快 ,最快速度为图3中 。且最快与最慢两者相差177.3 mm/s,所以料头向左侧弯曲。
图9模拟结果,B-B视图显示,从B-B方向看过去,型材向左边弯曲;
C-C 视图和B-B视图方向刚好相反,显示的弯曲方向也相反。表明模拟结果和试模结果是一致的。
图9 B-B 料头流速分布和变形图 (向左边稍微弯曲)
图10 从C-C 视图方向看过去的料头(向右边稍微弯曲)
3.2 根据模拟结果进行优化设计
根据以上结果进行综合分析结果对初始设计方案进行修改。对二级导流(二级导流二维图如下图11所示)进行优化修改,如下图12所示:
图11 模具二级二维图
图12 优化设计示意图
3.3 优化结果分析
根据优化好的设计加工模具,并上机试模,通过跟踪发现,根据后续跟进,优化后模具生产出的型材得到优化,料头较为平整。
从实际生产中可以找到很多型材,未优化的时,大多出现料头不平,单孔中快慢相差大、多孔出料速度差距较大等缺陷,如图13所示。由此可见使用有限元软件进行优化设计是有有必要的。
图13 未经优化产出的料头
4 结论
(1)利用HyperXtrude平台能够有效地对挤压过程进行仿真模拟,可节省大量设计时间,模拟结果对实际生产具有很高的参考价值。
(2)运用有限元分析软件对挤压过程进行模拟,可有效减少试模次数,发现凭借经验难以发现的结构缺陷,从而降低企业成本,提高型材质量。
参考文献
[1] 宋杰. 薄壁铝型材挤压过程仿真及模具优化设计[D]. 湖南省长沙市.中南大学.2006.
[2] 李积彬,伍晓宇,刘科胜.铝型材挤压模具的3D优化设计[J],机械设计,2000,6(6):29-32.
[3] 盛伟,谢配良,陈胜. ANSYS二次开发软件在塑性成形模拟中的应用[J]. 机车车辆工艺,2002(6):24-27.
[4] 于沪平,彭颖红,阮雪愉. 平面分流焊合模成形过程的数值模拟[J]. 锻压技术,1999年,24(5): 9-11.
[5] 刘汉武,丁桦,崔建忠. 铝型材挤压分流组合模有限元分析与计算[J]. 模具工业,1999年,(4): 9-11.
上一页12下一页
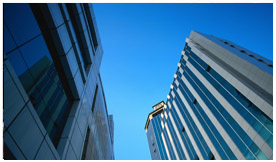
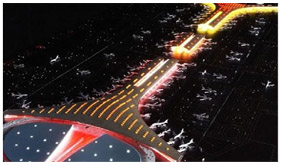
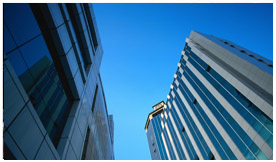
[摘 要]点支承开孔玻璃板承受垂直于板面的均布荷载时,开孔周围分布着较大的集中应力,显著影响着玻璃板的承载性能。目前国内外对于点支承单层玻璃板孔边应力的研究较多,但关于中空玻璃板孔边应力的研究尚不多见。本文利用有限元方法求解四点支承中空